This project focuses on optimizing a bottling process line involving the bottle packaging of bio-culture media, and ultimately lowering the costs associated with bottle leakages. The bottling process line includes the capping machine and conveyor, as well as the torque readout monitor. The torque applied to the bottle cap within the packaging process is the primary opportunity for quality improvements for the reduction of bottle leakages. The costs associated with bottle leakages were estimated to exceed $617,000 over the 2018 year for the project sponsor.
A screening design of experiments was used to determine which aspects of the machine were significant to for the application of torque. The observations and results from the screening design led to three primary design improvements: improving friction disk wear rate, creating optimized machine adjustment settings, and the introduction of an induction sealing solution as an addition to the bottling process line. These alternatives are explored and analyzed to determine their effects on the capping and packaging of bottles, with an estimate of lowering the bottle leakage rate. With an economic analysis to compare the three alternatives, it is concluded that the optimized adjusted settings solution achieves results immediately with a low implementation threshold, but with the recommendation for introducing an induction sealer to the bottling process long term.
A screening design of experiments was used to determine which aspects of the machine were significant to for the application of torque. The observations and results from the screening design led to three primary design improvements: improving friction disk wear rate, creating optimized machine adjustment settings, and the introduction of an induction sealing solution as an addition to the bottling process line. These alternatives are explored and analyzed to determine their effects on the capping and packaging of bottles, with an estimate of lowering the bottle leakage rate. With an economic analysis to compare the three alternatives, it is concluded that the optimized adjusted settings solution achieves results immediately with a low implementation threshold, but with the recommendation for introducing an induction sealer to the bottling process long term.
Example of Bottle Torquing Machine Operation
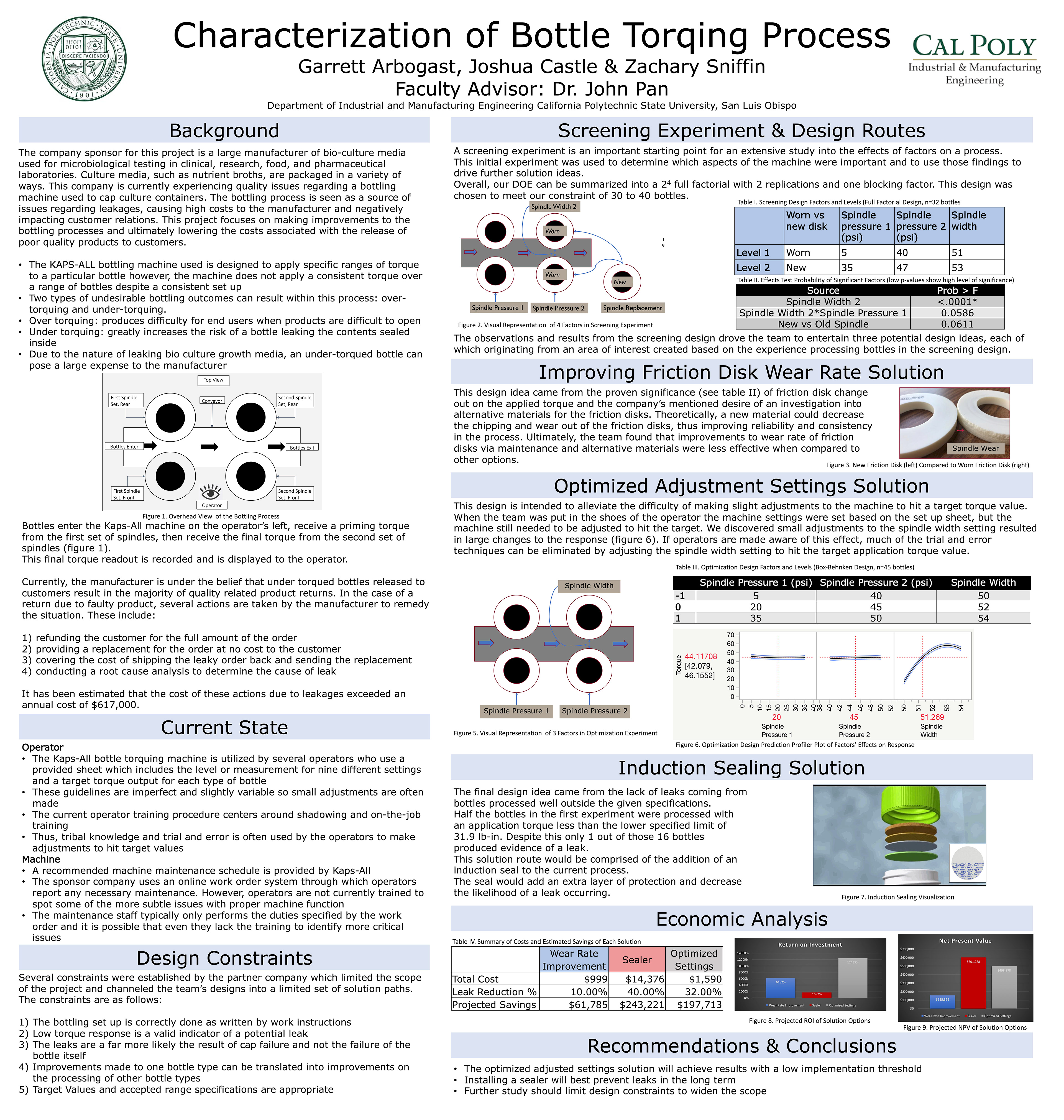
A few of the main machine settings and torque readout monitor
Leak testing equipment